Table of Content
Mark is also a co-host of the Custom Apparel Startups Podcast. If you’re a home embroiderer now, you’re already on your way to understanding how to use the larger industrial machines. For example, the Avance 1501C embroidery machine has an updated touchscreen control panel like many of the pricier home machines do. This type of commercial machine allows for quick turnaround for products out of large shops or smaller home-based startups.
Alternatively, take a photograph and transfer it to your computer. If you're designing a shirt for a specific activity or event, there are specialized options to consider. For example, if you're planning a hike or a trip to the gym, a moisture-wicking performance shirt will keep you cool and comfortable. If you're hitting the beach, a lightweight and breathable linen shirt will help you stay cool in the sun.
Like us for tshirt design tips, promos, and the discounts.
Use steady strokes to trace the chalk lines of your design. For an even bleach line, reload your brush every two inches. The fabric will quickly soak up the liquid so work quickly, but with a steady hand. Peel the contact paper off of the t-shirt when the paint is dry. You will now have a stenciled on t-shirt.You can use the stencil to make another shirt if you want more than one stenciled t-shirt.
Secure the shirt to the cardboard with elastics or small clips. This will keep the cardboard from slipping while you bleach paint. Always protect your eyes, clothing, and any open cuts from coming into contact with bleach. If possible, have a friend hold the screen down tight while you spread the ink. Specific directions for the light needed should be on the packaging of the purchased emulsion.
OnDemand - Customization
Printing on clothes and t-shirts has never been easier or more accessible. Technology has improved garment printing so much so that even home crafters can print photo-quality images on their clothing at home. Even so, if you are wondering how to print on t-shirts, there is a lot to learn about the different types of shirt printing methods before you start cranking out designs. You will need an inkjet printer, an iron, a cotton underlay , and scissors. Purchase transfer paper from stationary or craft stores.
Make a line on the mid-point of the neck binding and the neck hole’s midpoint on the front side. Measure and cut a strip of fabric at 4cm wide and 45cm long. Ensure you adjust your cutting in terms of length, stretch, and width-wise. Sew the pinned shoulder edges and join two separate pieces together. You can also use some heavy books or sewing weights to hold the shirt.
Valentines for Kids: Gumball Machine Free Valentine Card
Insert the pins straight down via a seam and onto a paper for the sleeve seam. Make sure you keep the pins no further than 1 inch apart. Neckline, insert the pins via a seam joining the back neckline to the collar. The pins you insert on the shoulders, sides, and bottom hem don’t need to be precise since their primary purpose is to hold the shirt. The idea here is to help you make your own clothes. Refine the pattern as per your needs and try again and again.
They will give you the ideal temperature settings and amount of time you will need to apply the heat. With your design ready to be transferred to the t-shirt or other fabric you should position the print where you want it and apply the heat and pressure for the specified time. There are a few things to consider when making prints using heat transfer paper. It is important to note that the results will not be as vibrant as other methods when transferring to dark fabrics and you need to be sure to use opaque transfer paper. Lastly, you need to trim any excess paper from your printed design, otherwise, you will transfer unnecessary material onto the shirt which is noticeable in looks and feel.
Place the cardboard inside your shirt and smooth out the area again.Cardboard works well because it’s flat and won’t let the ink bleed through to the other side of the shirt. Plus, when you’re done, you can just throw it away. Iron the shirt until you’ve removed all wrinkles, especially on and around the area you plan to print on. Any paper you leave around the image will show up as a thin film on the shirt. To create a clean image, cut out the image.To get an accurate cut, use a ruler and an Exacto knife.
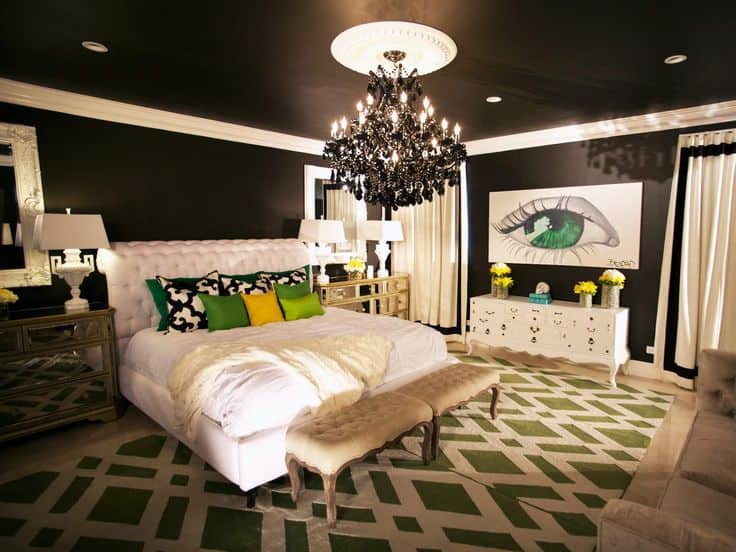
When it comes to expressing yourself, creating custom t-shirts is one of the best options. Whether you have beautiful artwork, a special photograph or any other type of design that you’d like to showcase, printing it on a t-shirt is a great option. Making your own shirts also works well when you need custom apparel for a team, group or organization. Yes, it literally means you print directly on the shirt.
Consider investing in some extra supplies just in case your first attempt don’t turn out quite as you’d hoped. Keep in mind digital printing is the simplest way to make a lot of t-shirts at once. Screen printing, stenciling, and bleach painting at home are good methods if you want to make a few t-shirts.
Each layer must dry before moving on to the next color and can be flash dried to save time. You also need to make sure you determine the order of your screens if any of the colors overlap. Once you have Printed each layer and they have dried you can now set the ink with heat.
– Do not iron directly on transferred image after it has been applied to the garment. Make sure that you are using a high-quality image. Print out your design on a regular piece of paper, to test out how it will look on the shirt. When you have created your design, import it to the software program that came with your vinyl cutter to prepare for cutting the vinyl. Begin cutting the design for each color and set them aside, you can also assemble the design to track your progress.
Place your negative on the inked part of the shirt. You can press down your negative onto your shirt to help it stick to the dyed area.Smooth out the area with your hand. You want your negative to make good contact everywhere with the dye. Insert a piece of foam core or cardboard into your shirt.
This method is very popular among anyone wanting to make shirt prints at home but it is also used by professionals as well in certain circumstances. This method can print colorful complex images that easily that is cost-effective and requires little to no special setup. The feel of heat transfer prints is not as soft as other t-shirt printing methods. Plastisol has the same limitations of screen printing consider the transfers are screened onto paper. This means gradients and multicolor limitations exist with this method. Also, the heat press method has a high startup cost, which makes screen printing the best option for beginners and budget-minded folks.

It’s best to remove the negative in a space that isn’t very bright.Removing the negative in subdued lighting will help to keep the print intact. Once you’ve covered the area you no longer need your frame.You can keep the frame on if you used tape and you think some of the dye may have bled through. And run your fingernail along the taped edges if you used tape to ensure there are no gaps.
No comments:
Post a Comment